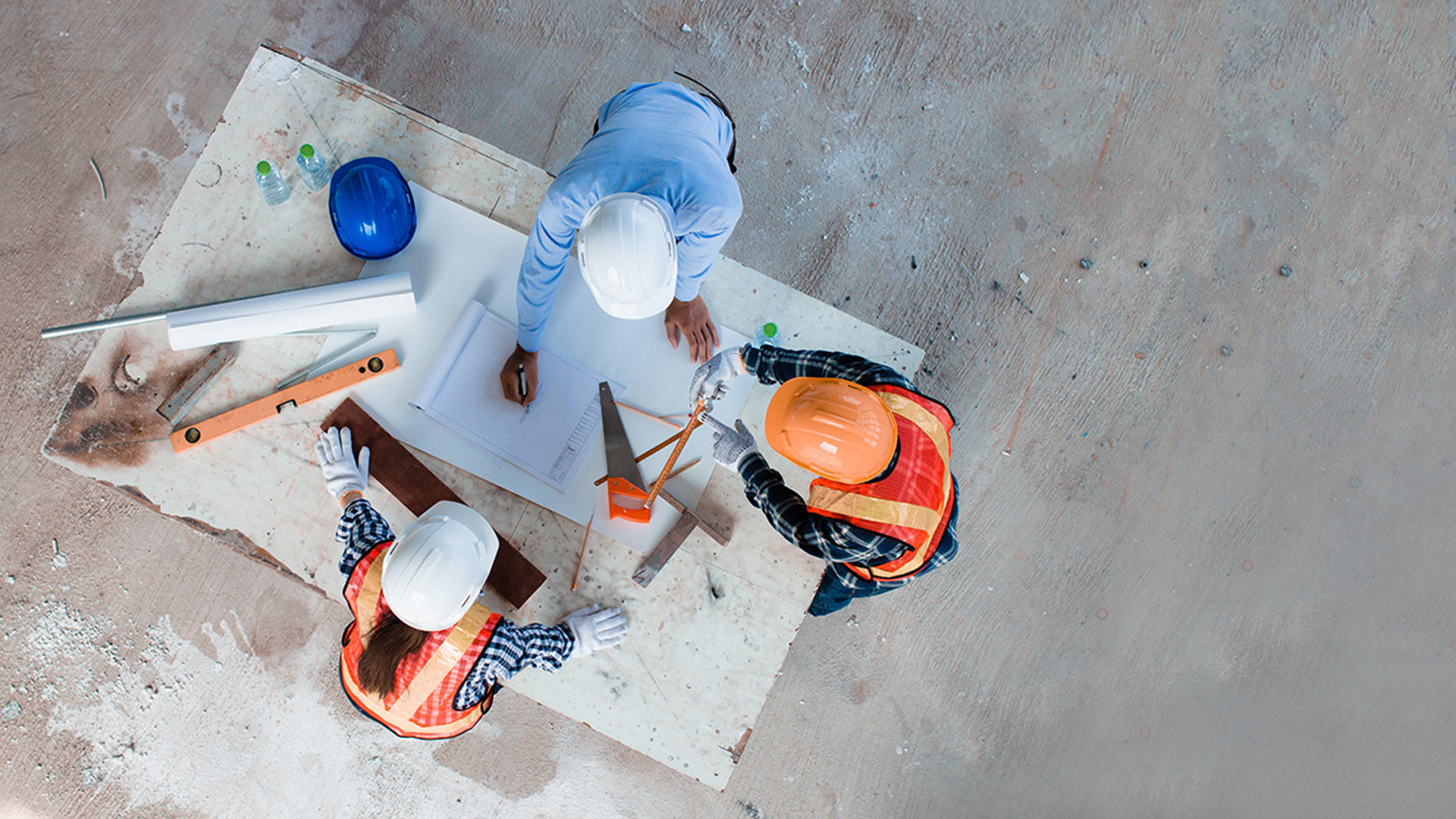
Designing for Safety
As design professionals, there are multiple steps we take during a project to maintain safety as a top priority. Thinking proactively about safety during the design process has an incredible impact on the wellbeing of people as well as influencing success in other areas not usually associated with safety.
The Case for Safety
People are a company’s most valuable resource. People provide customers with services, manufacture goods, promote the company brand, and differentiate a great place to work from a good place to work. Company success is inherently tied to the satisfaction of the team, and safety is a key component.
According to Great Place to Work's “100 Best Companies to Work For,” there is a major relationship between safety and employee morale. 96% of employees at the top 100 best companies rated their workplace as physically safe. When employees feel safe in their workplace, morale is higher along with attraction and retention.1
The quality and wellbeing of your workforce also contributes to a company’s success.
Aluminum company Alcoa is a shining example of the impact intentional safety design can make. During Paul O’Neill’s tenure as CEO, he began focusing the organization on becoming the world’s safest company with a goal of “zero harm” or “no accidents”. The results were documented as follows:
- Annual earnings went from $.20 per share in 1994 to $1.41 in 1999.
- Sales grew an average of 15% per year in the same period.
- By 2000, it was five times safer to work at Alcoa than ten years earlier.2
When analyzing the impact of safety, direct costs have immediate financial implications and can include:
- Medical expenses
- Litigation expenses
- Civil liability damages
- Property losses
- Workers’ compensation payments
Indirect costs are often overlooked in importance and can carry a far greater financial impact. In a survey of financial decision makers, it was estimated that the average ratio is $2.12 in indirect cost for every $1 spent on direct costs.3
Prevention Through Design
According to the National Institute for Occupational Safety and Health (NIOSH), one of the best ways to prevent and control occupational injuries, illnesses and fatalities is to “design out” or minimize hazards and risks early in the design process. NIOSH is leading a national initiative called Prevention through Design (PtD) to promote this concept and highlight its importance in all business decisions. PtD can be defined as addressing occupational safety and health needs in the design process to prevent or minimize the work-related hazards and risks associated with the construction, manufacture, use, maintenance and disposal of facilities, materials and equipment.4
PtD incorporates strategies found in the hierarchy of controls (shown below), which ranks effectiveness of control strategies implemented in the workplace.
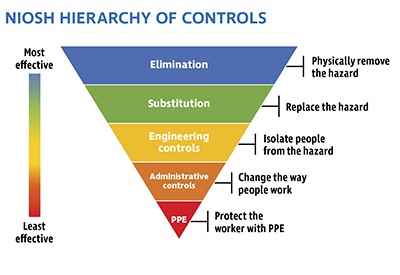
Due to the nature of our work, design professionals are often in an advantageous position to embed more effective strategies into the design process. This is especially true at the onset when safety is made a priority consideration and made part of the collaborative effort to frame the client’s vision. In some cases, hazards can be completely designed out. To some, PtD sounds like a lot of extra work and required expertise, but it is not. The PtD process is inherent to what we should be doing for every project; engaging, listening and then acting upon the client’s vision for their facility. Broken down in steps, PtD can look similar to the following:
1. Identify Hazards and Users
Before design begins, potential hazards and the users of the equipment, process or space must be identified. Hazards can be physical, chemical, biological, ergonomic, or psychological, and they can vary depending on the context, environment, and task. Users can be any number of stakeholders including workers, customers, contractors, or visitors, and they can have different needs, preferences, and abilities. These can be identified through focused conversations with the client stakeholders.
2. Involve Stakeholders and Experts
Designing with safety in mind is a collaborative effort that attains greatest benefits through a wide range of stakeholders and experts at project onset. Client stakeholders and experts bring unique insights that positively affect safety considerations. Engaging with client safety professionals, engineers, and specialists in ergonomics and human factors is equally important. Their expertise can transform good designs into great, safe solutions. Great tools to focus on this includes workshops, focus groups, and prototyping, leading to designs that are not only safe but also practical and universal.
3. Standards and Principles
Designing with safety in mind also requires integrating safety standards and principles that are identified during engagement with client stakeholders for insight into equipment, process, or space safety. Standards can be a combination of legal requirements, industry best practices, or organizational insight. They can specify the minimum requirements or even specifications for the design. Our experts are well versed in principles of Universal Design, which specializes in removing potential physical and social barriers and improving safety outcomes.
4. Optimize
Designing with safety in mind does not mean compromising usability and performance. More accurately, safety can enhance usability and performance by making the equipment, process, or space more efficient, effective, and satisfying for the users. Usability refers to how easy, intuitive, and comfortable your equipment or process is to utilize in the space. Performance is about validating results of the design after construction.
PtD in Action
During a walkthrough of a paper recycling facility, ear plugs were required before entering the production floor. The design professional noticed that the main source of noise was a shredding machine used for preparing paper for recycling. By engaging the client and asking questions, the design professional identified that the shredder does not have to be regularly accessed during normal production. The designer also gained understanding of the maintenance requirements for the shredder during turnaround events and the clearances required.
With this information, the design for expansion included space around the shredder for sound dampening enclosure reducing the ambient noise levels to eliminate the need for hearing protection during normal operation. The enclosure also reduced the introduction of paper particulate into working areas, improving air quality and reducing combustible dust and fiber hazards. This created a safer, more optimized workplace that increased overall employee satisfaction.
When a consultant assists with design services at your site, safety of your team, equipment, and plant should be a priority. It should be an organic piece of the design process and a beneficial outcome when the design is constructed. Our team understands the Prevention through Design philosophy and have team members intimately familiar with what is required for your facility to operate safely and effectively.
References
1 Staying Safe: How Safety Affects Employee Retention. 30 November 2021. John Niemoller. EHS Management,Risk Management,Health & Safety. https://www.perillon.com/blog/staying-safe-how-safety-affects-employee-retention
2 Krause, r. (2001, february 21). Alcoa’s Paul o’Neill relied on analysis and safety to boost his company to the forefront. investors.com. retrieved october 17, 2013, from www.investors.com/NewsAndAnalysis/ Article.aspx?id=338019&Ntt.
3 Huang, Y., Leamon, t. B., courtney, t.K., deArmond, s., chen, P.Y., & Blair, M.f. (2009). financial decision makers’ views on safety: What sH&e professionals should know. Professional Safety, 54(4), 36-42.
4 https://www.cdc.gov/niosh/topics/ptd/default.html